VEX300T
CMEV air handling unit
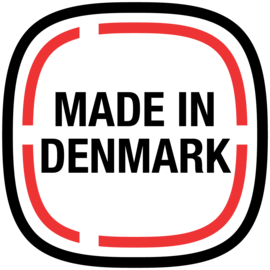
The range consists of 5 sizes, with an option for the EXact2 control system or prepared for a third party control system.
VEX300T has been construced with integral heating or cooling coils, which reduces the installation costs. It is also possible to choose filtration of the supply air.
The design is optimised for compactness, temperature efficiency, airflow and energy consumption. Despite being very compact in size, the unit is easy to service, e.g. for filter change, cleaning, etc.
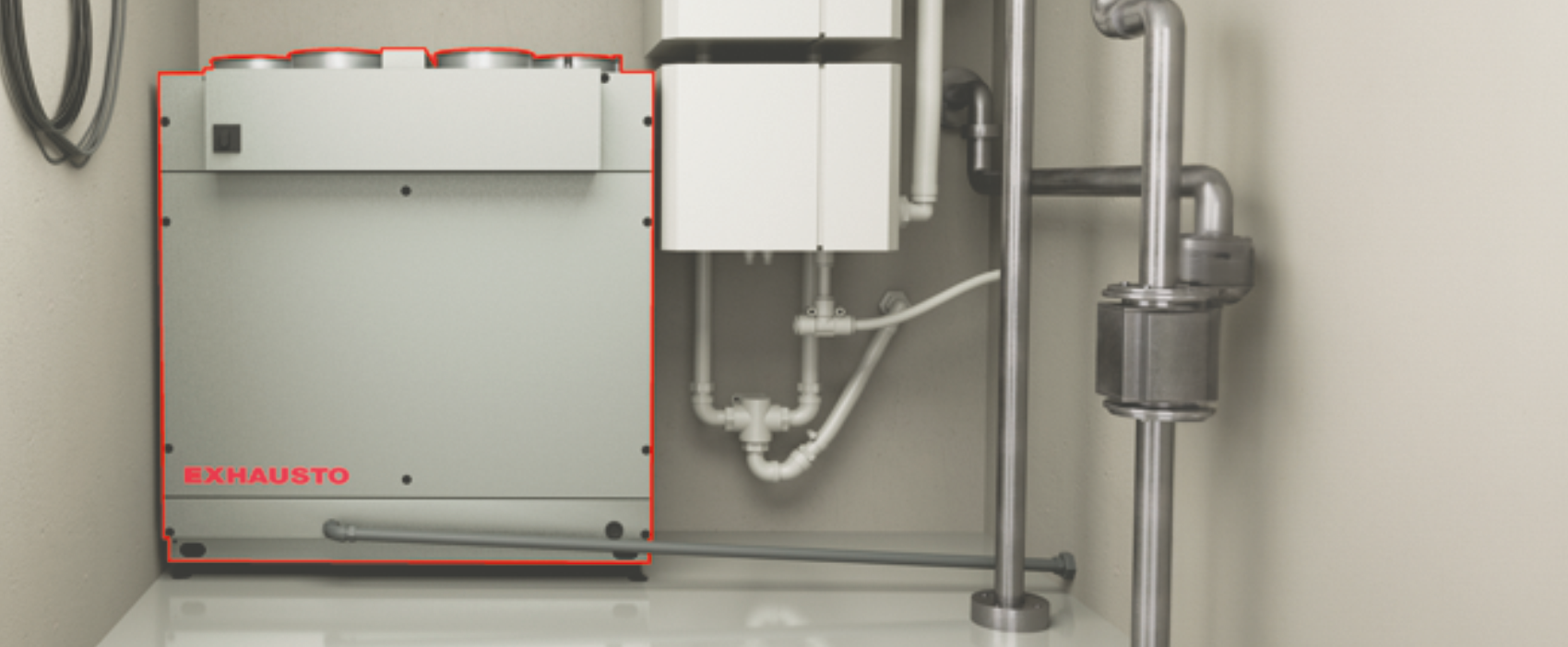
Product advantages
- Transport through 900-mm door possible
- High efficiency (up to 90%) AHU units
- Exclusive Aldes Smart Control System
- Optimal air quality and thermal comfort
- Vertical duct connection
- Selection of left or right side for supply air
- Configuration-specific electrical diagrammes are supplied with the unit (incl. accessories)
The VEX 300T brings fresh, filtered air into the building and recovers heat from exhaust air using its high-efficiency heat exchanger. The incoming air can be heated and/or cooled using a comprehensive range of coils.
-
1 decentralised model - up to 850 m3/h - in 2 versions:
- visible version (STD),
- semi-integrated version (INT) for installation in a suspended ceiling.
- Monoblock construction,
- insulation - 20 mm polyurethane for better noise attenuation,
- external finish: Aluzinc AZ185: class C4 anti-corrosion performance. Can be customised in pre-painted white (standard), anthracite grey, gold on request,
- vertical attachments for connection to ceiling or horizontal attachments for wall-mounted connections,
- EC motor and forward curve impeller,
- high efficiency counterflow heat exchanger (Eurovent AAHE),
- adjustable by-pass,
- ePM10 60% (M5) or ePM1 55% (F7). Coarse 60% (G4) pre-filters as accessory,
-
accessories:
- built-in CO2 sensor,
- built-in motion sensor with LED status indicator - PIR,
- built-in humidity sensor - HR,
- communication with webserver - WEBE,
- HMI user interface (for start-up and commissioning),
- caution: if the built-in CO2 sensor and the built-in PIR are selected, the unit is fully ready for use.
- Extremely compact design with top connection
- Integrated cooling/heating coil
- Very quiet product, emits minimal noise to the surroundings
- VEX300T must be located indoors and can be used for all purposes where the special top-duct construction will aid installation.
Available filters | Motor class in accordance with IEC TS 60034-30-2 | Current overload protection | Connection direction | Type of exchanger |
---|---|---|---|---|
ePM1 80% (F9), ePM1 55% (F7), ePM10 65% (M5), Coarse 65% (G4). |
IE4 (Super Premium Efficiency) |
Built-in |
Top |
Counterflow |
References | Max. Total efficiency (A-D) (%) | Efficiency level requirements | ECO efficiency level during optimal operating point | Overload protection |
---|---|---|---|---|
VEX310T | 47,9 |
62N (2015) |
78,4N |
Built-in |
VEX320T | 46,9 |
62N (2015) |
68,5N |
Built-in |
VEX330T | 60 |
62N (2015) |
79,4N |
Built-in |
VEX340T | 61,5 |
62N (2015) |
80,2N |
Built-in |
VEX350T | 67,5 |
62N (2015) |
76,7N |
Built-in |
Conditions:
- Density = 1.2 kg/m3
- Pressure ratio < 1.11
- other points in acc. with EC327/2011 (see product instructions)
References | Voltage input | Regulation | Control signal with control system | Control signal with third party control system | Fluid temperature (air) | Ambient temperature range |
---|---|---|---|---|---|---|
VEX310T | 1 x 230 V |
Variable via motor control (MC) |
Modbus |
0-10 V DC |
-40°C...+40°C |
-30°C...+50°C |
VEX320T | 1 x 230 V |
Variable via motor control (MC) |
Modbus |
0-10 V DC |
-40°C...+40°C |
-30°C...+50°C |
VEX330T | 1 x 230 V |
Variable via motor control (MC) |
Modbus |
0-10 V DC |
-40°C...+40°C |
-30°C...+50°C |
VEX340T | 1 x 230 V |
Variable via motor control (MC) |
Modbus |
0-10 V DC |
-40°C...+40°C |
-30°C...+50°C |
VEX350T | 1 x 230 V |
Variable via motor control (MC) |
Modbus |
0-10 V DC |
-40°C...+40°C |
-30°C...+50°C |
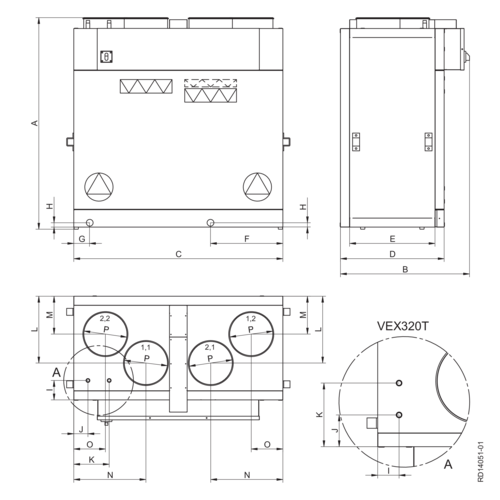
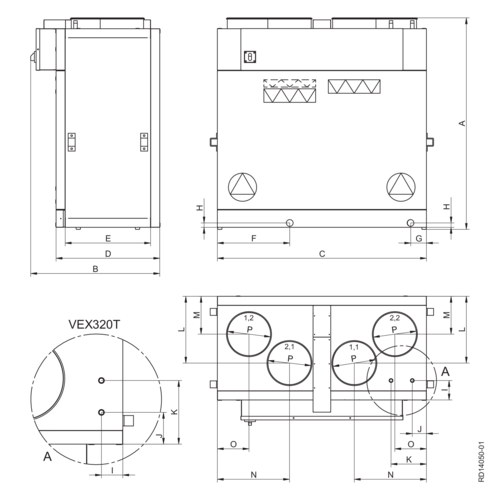
References | A (mm) | B (mm) | C (mm) | D (mm) | E (mm) | Ø connection (mm) | Weight (kg) | Weight for transport |
---|---|---|---|---|---|---|---|---|
VEX310T | 1215 |
754 |
1200 |
595 |
490 |
250 |
157 |
86 kg (excl. doors, heat exchanger and fans) |
VEX320T | 1215 |
1024 |
1200 |
865 |
760 |
315 |
204 |
124 kg (excl. doors, heat exchanger and fans) |
VEX330T | 1474 |
1092 |
1500 |
932 |
827 |
315 |
265 |
158 kg (excl. doors, heat exchanger and fans) |
VEX340T | 1775 |
1092 |
1900 |
932 |
827 |
400 |
345 |
194 kg (excl. doors, heat exchanger and fans) |
VEX350T | 1825 |
1149 |
2400 |
990 |
885 |
500 |
415 |
245 kg (excl. doors, heat exchanger and fans) |
References | Minimum airflow | Max. airflow ErP (m³/h) | Max. airflow (m³/h) |
---|---|---|---|
VEX310T | 80 |
550 |
550 |
VEX320T | 100 |
1090 |
1225 |
VEX330T | 200 |
1775 |
2150 |
VEX340T | 350 |
2375 |
2460 |
VEX350T | 400 |
3675 |
4095 |
References | Max. exchanger output (%) |
---|---|
VEX310T | 94 |
VEX320T | 94 |
VEX330T | 94 |
VEX340T | 99 |
VEX350T | 100 |
The counterflow heat exchanger in VEX300T is made of aluminium. Its design ensures the ratio between heat recovery and pressure drop is optimumally distributed.
I.e. extremely high temperature efficiency is achieved at low levels of energy consumption.
- 80-85% efficiency without condensation
- Up to 94% efficiency with condensation
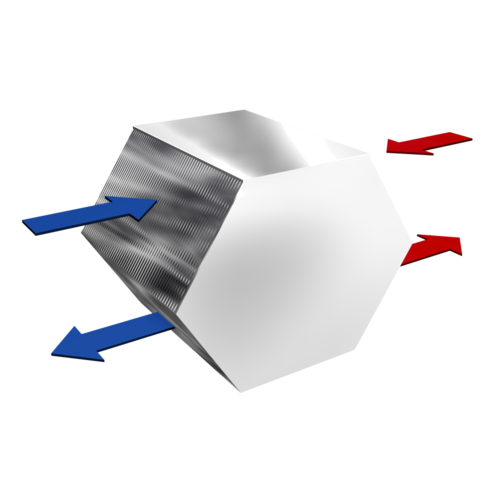
The combination of a modern EC motor and an optimised centrifugal impeller delivers extremely low energy consumption and greater output at the same time.
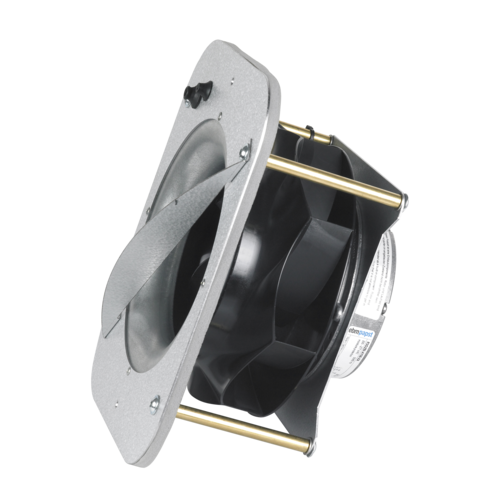
An energy label that states the energy class of the air handling unit in relation to defined operating conditions is available via our product calculation programs.
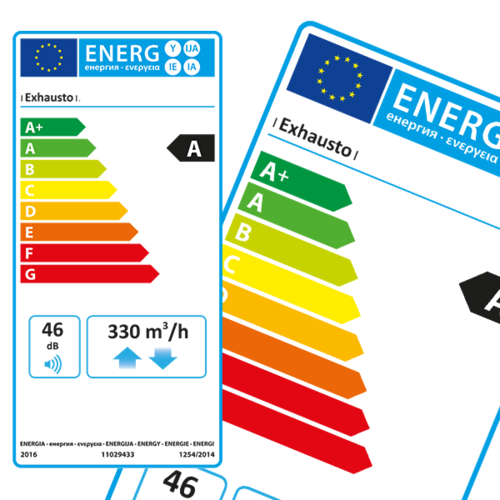
References | Voltage (V) | Frequency (Hz) | Electrical coil voltage 1 | Max. power of electrical coil 1 (kW) | Max. power of electrical coil 2 | Max. current consumption SINGLE-PHASE 230 V (A) | Maximum current - unit (A) | Max. electrical output of unit (kW) |
---|---|---|---|---|---|---|---|---|
VEX310T | 1x230 |
50 |
3x400 |
1,68 |
3,9 |
3,9 |
3,9 |
0,5 |
VEX320T | 1x230 |
50 |
3x400 |
3,37 |
7,81 |
4,7 |
4,7 |
1,0 |
VEX330T | 1x230 |
50 |
3x400 |
5,61 |
10,41 |
7,3 |
7,3 |
1,7 |
VEX340T | 1x230 |
50 |
3x400 |
7,49 |
14,96 |
7,3 |
7,3 |
1,75 |
VEX350T | 1x230 |
50 |
3x400 |
12,65 |
22,76 |
13,5 |
13,5 |
2,7 |
- : Complies with eco-design regulation 1253/2014 and energy labelling regulation 1254/2014 for ventilation. Energy classes:
- : Yes
- : BAT-TH-126
Cabinets are made from Aluzinc® AZ185 class C4 in accordance with EN/ISO12944-2 and insulated with 50 mm mineral wool. This results in low noise emissions to the surrounding environment/installation room.
The panel design minimises the formation of thermal bridges in the unit.

The motor sections are mounted in vibration dampers, which reduces noise in the ducts and eliminates the need to fit flexible connections between the unit and the duct system.
The motors are of type EC and are extremely efficient. They comply with the requirements of the Ecodesign Directive.
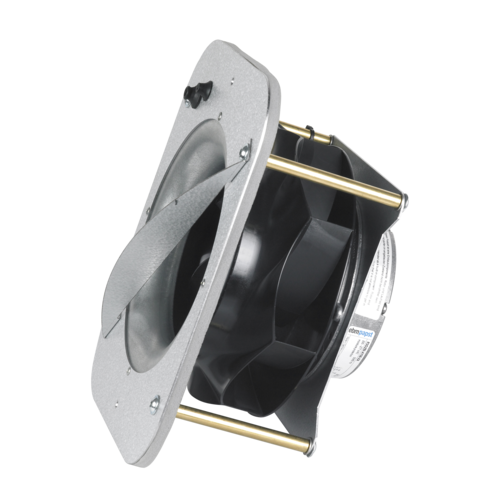
VEX300T is equipped with an optimised centrifugal impeller with backward curved blades.
The wheel is made from a composite material and its shape provides great performance with low energy consumption.

The VEX300T range is supplied with an integral heating coil or cooling-heating coil
HE: Electric heating coil (requires airflow control, accessory - AFC)
HW: Water heating coil
CW: Cooling-heating coil (option for cooling in summer and heating in winter)
DX: Cooling-heating coil (option for cooling in summer and heating in winter)
See more about cooling/heating coils under the technical data for the size in question.
Note: It is also possible to order the VEX300T without cooling and/or heating coils
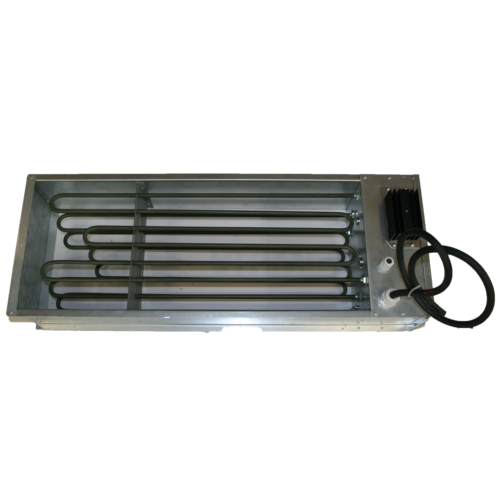
The easily accessible connection box with built-in isolator switch and control fuses ensures easy access for connection and adjustment. Read more about electrical connection in the guide “Electrical guide for VEX310-350T”
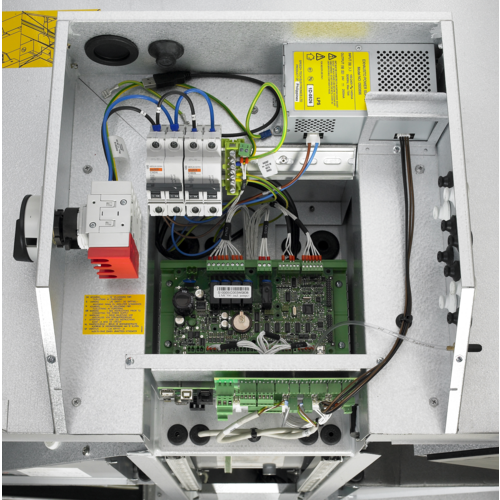
Panel filters for supply air and extract air– the filters are easy to replace.
The filters are available in the following filter classes: ePM1 80% (F9), ePM1 55% (F7), ePM10 65% (M5) and Coarse 65% (G4).
See filter size under technical data for the individual VEX size.
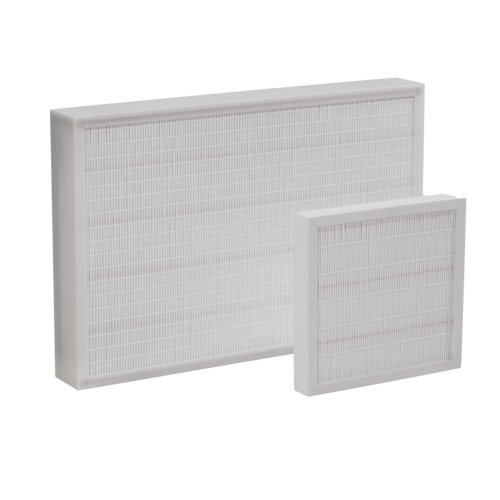
With some projects, limited space means that internal transport of the air handling unit is difficult or impossible. This is why the VEX300T is available as a SPLIT version. It means that the air handling unit can be assembled and tested at the factory as normal – just without sealant. The air handling unit can therefore be easily taken apart at the installation site, transported as single sections, assembled, sealed and commissioned.
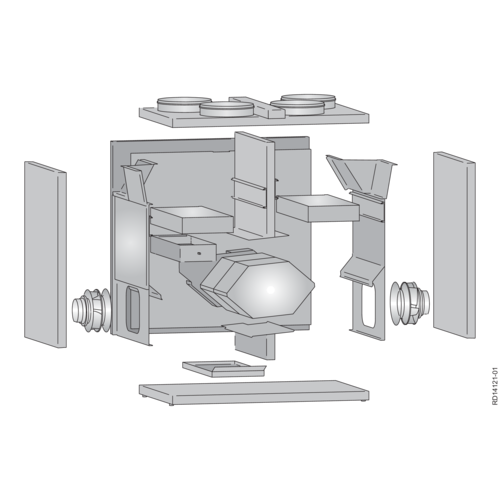
It is possible to insert a 48-mm filter ahead of the standard filter on the supply air side. Placing a coarser filter in front of a finer filter reduces soiling on the finer filter. Depending on the outdoor air and the desired quality of the supply air, this can be a good idea/option.
The filters for pre-filtration are available in the following filter classes: ePM1 55% (F7), ePM10 65% (M5) and Coarse 65% (G4).
Pressure drop, etc. can be calculated in the product selection programme EXselectPRO.
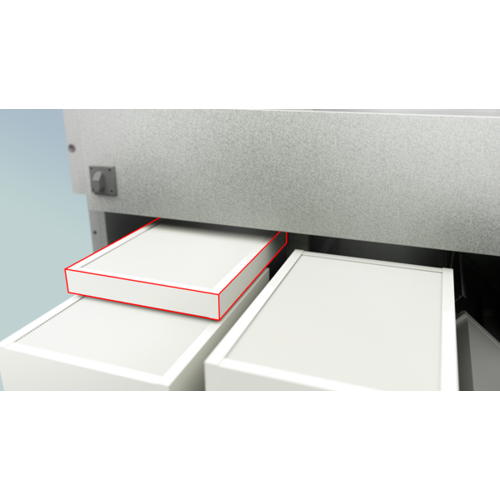
The VEX300T is designed with de-icing bypass. If there is a risk of icing, then a certain amount of outdoor air will bypass the heat exchanger and go directly to the after heating coil. This increases the demands on the heating coil’s output. However, it avoids a costly preheating coil. The drawing below is an example of a de-icing situation, where 20% of outdoor air is directed through the bypass damper.
Heating coil and de-icing function:
The de-icing situation is shown above, a heating coil is included here. This is completely necessary, in order for the de-icing function to function correctly. Without the heating coil, the de-icing process will cause the temperature of the supply air to fall and sooner or later the VEX unit will stop because of icing.
The heat exchanger has two forms of frost protection: temperature-controlled or pressure-controlled. The actual de-icing can take place in several ways, depending on whether an after heating coil has been fitted. A post-heat surface is always recommended to maintain continuous ventilation.
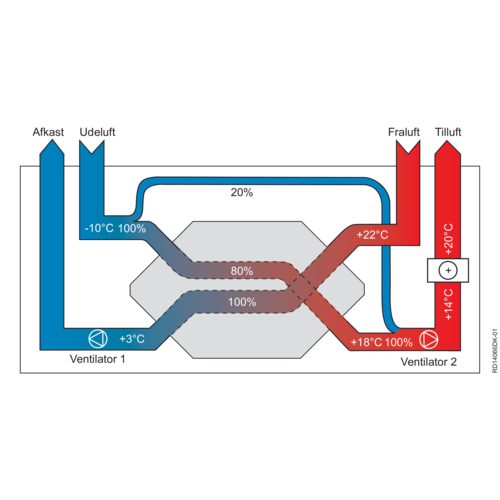
The control system has temperature-controlled frost protection as standard. It is an inexpensive solution and provides sufficient frost-protection in some situations.
A temperature sensor is fitted inside the heat exchanger and if the temperature falls to a pre-set value, de-icing begins. This temperature level is factory set to 0 °C but it can also be changed to a new value via the control system.
Temperature-controlled frost protection triggers the de-icing process even if there is no ice in the heat exchanger.

The control system monitors the actual airflow and also the pressure drop across the heat exchanger. If ice forms in the heat exchanger, the pressure drop across the heat exchanger will increase and when it exceeds a pre-set value, de-icing begins.
Pressure-controlled frost protection only starts de-icing when ice has actually formed, regardless of whether there are sub-zero temperatures.

Documents
-
VEX310T-350T EXcon/EXact EC Declaration of ConformityConformities203 KB
-
VEX310T-350T-X, EC Declaration of ConformityConformities203 KB
-
VEX310T ERP/ECO DeclarationConformities344 KB
-
VEX320T ERP/ECOdesign DeclarationConformities343 KB
-
VEX340T ERP/ECO-design declarationConformities346 KB
-
VEX350T ERP/ECOdesign DeclarationConformities346 KB
-
VEX, Siphon - pressure side, installation guideManuals641 KB
-
VEX310T 1 and 3 phased EXcon connection diagramCAD drawings633 KB
-
VEX320-350T 1 phased EXcon connection diagramManuals581 KB
-
VEX320-350T 3 phased, connection diagram (no control system)Manuals639 KB
-
VEX, Siphon - suction side, installation guideManuals633 KB
-
VEX, SiphonHE - frost protection, installation guideManuals598 KB
-
VEX310T-350T-X without controls, mechanical instructionManuals6 MB
-
VEX310T-350T with EXact2, mechanical instructionManuals6 MB